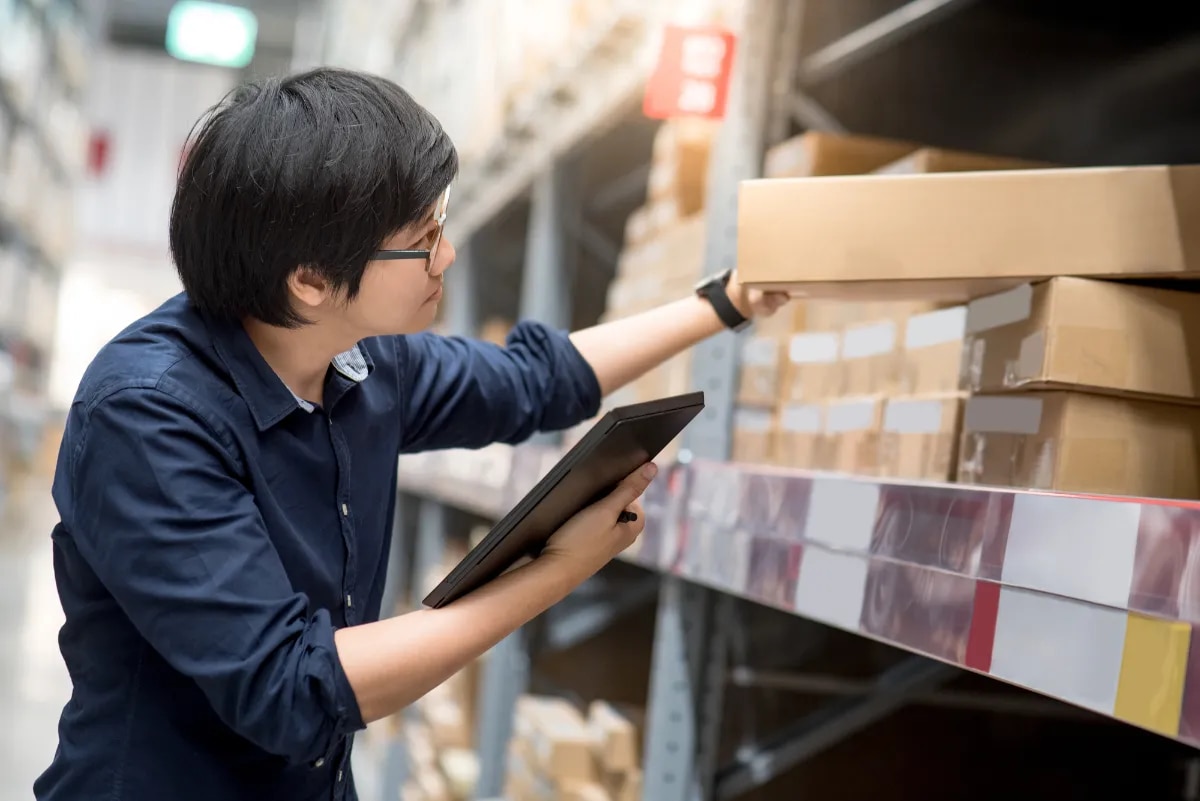
先入れ先出しのメリットと注意点|在庫管理を効率化するコツは?
こんにちは。物流に関する知識をまとめたメディア「ピックゴー物流コラム」編集部です。
在庫管理は、倉庫業務における重要な業務のひとつです。しかし、在庫管理の最適化が進んでいない企業も多く、滞留在庫の増加によって販売できた商品を廃棄しているケースも少なくありません。
そこで導入を検討していただきたいのが「先入れ先出し」という考え方です。先入れ先出しを徹底することで入荷した順番で商品を出荷でき、滞留在庫の削減や不良品の発生防止につながります。今回は、先入れ先出しのメリットや注意点、在庫管理を効率化するためのポイントを解説します。
目次[非表示]
- 1.先入れ先出しの基礎知識
- 1.1.先入れ先出しとは?
- 1.2.「先入れ先出し」と「先入れ後出し」の違い
- 2.先入れ先出しを行うメリットと注意点
- 3.先入れ先出しを効率化するためのポイント
- 3.1.マニュアルを作成し社内で徹底する
- 3.2.適正在庫を維持する
- 3.3.3Sを意識する
- 3.4.商品の配置方法を工夫する
- 3.5.定期的に商品状態のチェックを行う
- 4.先入れ先出しを実践して在庫管理の効率化を進めよう
先入れ先出しの基礎知識
先入れ先出しは、「先入先出法」とも呼ばれる在庫品の管理手法です。商品の品質維持に役立つため、厳密な在庫管理が求められるECや製造業などの物流現場で取り入れられています。まずは、先入れ先出しの基礎知識や先入れ後出しとの違いを解説します。
先入れ先出しとは?
先入れ先出しとは商品を出荷する際、先に入庫したものから順に出庫する管理方法。英語では「First In First Out」と表記され、「FIFO」との略語で使用される物流用語です。賞味期限がある食品や劣化しやすい製品の品質管理に用いられることが多く、在庫管理の基本的なルールとして小売業や製造業などで広く導入されています。実際の作業は、商品の入荷後に古い在庫を棚から取り出し新しい商品を奥に配置、古い商品から出荷といった流れで進めるのが一般的です。
「先入れ先出し」と「先入れ後出し」の違い
先入れ後出しとは商品の出荷時に、後から入庫した新しいものから順に出庫するという意味です。英語では「Last In First Out」と表記され、「LIFO」と略されることもあります。先入れ先出しとは出庫の順番が異なるのが特徴です。先入れ後出しは倉庫作業を簡略化でき、購入コストの変動に対応しやすいなどのメリットがあります。一方デメリットは、滞留時間が長期化することで商品の品質低下や破損のリスクにつながる点が挙げられます。
先入れ先出しを行うメリットと注意点
先入れ先出しには、不良在庫の発生防止や保管場所の整理整頓につながるなどのメリットがある一方、作業工数や管理するデータの増加といった懸念点も少なくありません。ここでは、先入れ先出しの導入によるメリットと注意点をご紹介します。
メリット
- 不良在庫の発生防止に役立つ
先入れ先出しを徹底することで倉庫内の商品の滞留時間を減らし、劣化を防止できるため、不良在庫の発生防止に役立ちます。不良在庫とは売れる見込みがなく、経済的な損失につながるおそれのある在庫のことです。具体的には消費期限切れや劣化した状態の不良品、欠陥品などが該当します。不良品の販売は、ユーザーからのクレームや企業ブランドのイメージ低下の原因となるおそれがあるため注意が必要です。また、先入れ先出しによって不良在庫の発生を防止できれば廃棄や値引き販売のリスクを減らすこともでき、利益の最大化も見込めます。
- 倉庫スペースの整理整頓がしやすくなる
先入れ先出しを行うには商品の入荷日や出荷日を管理する必要があるため、自然と保管スペースの整理整頓につながります。棚卸のタイミングでもスムーズに在庫数を確認できるようになり、業務の効率化を実現できます。
- 出荷時間の短縮につながる
先入れ先出しによって常に古い商品が棚の手前に配置されていれば、ピッキング作業を効率化でき、出荷時間の短縮につながります。ECでは受注から配送までのスピードが重視される傾向にあり、顧客満足度の向上には先入れ先出しの徹底が重要です。
注意点
- 作業工数が増加する
先入れ先出しでは倉庫内に商品を入庫する際、「古い商品を一度取り出す」「取り出した商品を元に戻す」という作業が発生するため、作業工数の増加が懸念されます。先入れ後出しの場合、古い商品の前に新しい商品を保管するだけで入庫作業は完了します。先入れ先出しでは作業員の手間を省くために在庫管理システムを導入するなど、効率化施策を模索することが大切です。
- 管理するデータ量が増える
在庫管理に先入れ先出しを取り入れるには、商品名や商品番号だけでなく製造日や使用期限などのロット情報を詳細に管理する必要があります。商品管理の手間が増える傾向にあるため、オペレーションが最適化されていないと作業効率が低下するおそれがあります。
- 商品によっては運用が難しい場合がある
明確な使用期限が設定されていない商品は、時間の経過だけが劣化の原因ではないため、先入れ先出しがあまり効果を発揮しないケースも考えられます。例えばアパレルの商品やインテリア雑貨などは、食品や医薬品と比較して先入れ先出しに適さないとされます。取り扱う商品の種類に応じて先入れ先出しの運用を見直すことが重要です。
先入れ先出しを効率化するためのポイント
先入れ先出しは、一見簡単に見えるものの課題も多く、ただ導入しただけではかえって保管効率が下がる可能性があります。在庫管理を自社の強みに変えるには、合わせて以下のような効率化施策も実践しましょう。
マニュアルを作成し社内で徹底する
倉庫内業務は作業ごとにスタッフが分かれているケースが多いため、先入れ先出しに関するルールがあいまいだと個人の判断で作業してしまい、誤出荷や業務効率の低下につながるおそれがあります。事前にマニュアルを作成しておくと、アルバイトや派遣社員など作業に慣れていないスタッフが現場に入る場合でも指導しやすくなります。マニュアル作成後は定期的に見直しを行い、現場の状況に合わせて最適化を図ることが大切です。
適正在庫を維持する
在庫量が過剰になると管理するデータや作業工数が増えて作業員の負担が増すため、先入れ先出しが機能しなくなり、商品の劣化や使用期限の見落としなどが生じる可能性があります。これを防ぐには適正在庫を維持し、先入れ先出しを行いやすい環境を整えることが重要です。在庫管理システムや倉庫管理システム(WMS)の導入は、手間の削減や入力ミスの防止などに役立ちます。
3Sを意識する
3Sとは物流業務における整理・整頓・清掃の3つの工程を指します。倉庫内が雑然としていると商品の保管場所や状態の迅速な把握が難しくなり、不衛生な状態では商品の劣化につながるため、先入れ先出しには3Sの徹底が重要です。
商品の配置方法を工夫する
先入れ先出しによる作業工数の増加を抑えるには、商品の配置方法の見直しが効果的です。代表的な手法にはロケーション管理とカラーシール管理の2つがあります。
ロケーション管理は、倉庫内のどのエリアにどの商品を保管するのかを決める管理手法のこと。商品と保管場所を完全にリンクさせる「固定ロケーション」や、入荷した商品から倉庫内の空いているスペースで保管する「フリーロケーション」などがあります。
カラーシール管理とは一定の基準に沿って分類された商品に、それぞれ異なる色のシールを貼り管理する手法です。例えば商品を入荷月に応じて12種類に分類し、別の色のシールを貼ることで詳細な情報を確認せずに商品の鮮度を判断できるようになります。
定期的に商品状態のチェックを行う
明確な使用期限が設定されていない商品を扱う場合は、入荷日や出荷日の管理だけでなく定期的に商品状態そのものをチェックすることが大切です。入荷して間もない商品でも、想定より劣化が早い場合は出荷日を早めるなどすることで不良品を販売するリスクを減らせます。
先入れ先出しを実践して在庫管理の効率化を進めよう
先入れ先出しは、倉庫内業務における基本的な考え方です。先入れ先出しを徹底することで賞味期限や使用期限の近い商品から出荷でき、不良在庫の発生防止に役立ちます。
しかし、先入れ先出しには作業工数やデータ管理の増加などの懸念があるため、マニュアルの作成や3Sの徹底を通して作業の効率化を図ることが大切です。
配送コストの最適化や物流業務のアウトソーシングをご検討の際は、「ピックゴー」のカスタマイズ配送をご利用ください。貴社ビジネスに合わせた新しいモノの流れの構築をご提案いたします。